The Bright cage unloading system reduces bruises and wing damage by providing a smooth transfer of birds from the transport cage to the hanging belt with less down grade.
Its simplicity, reliability and longevity have been proven since the first installation in 1980, and because Bright Coop has continued to improve the system’s performance since it’s development 30+ years ago, the Bright cage unloading system has become the predominant method used in the USA, and now having systems in Mexico, Australia, Jamaica and Puerto Rico, the most widely used system in the world.
Each system is designed according to the plant layout and includes galvanizing, safety shutdown features and safety guards as standard equipment on new installations. The optional door closer and washer may be added to new or existing systems to reduce labor costs and significantly increase the life of your cages. Bright’s dedicated staff hand crafts each component of the system and has professionally installed over 200 units. Our experience facilitates a timely completion and startup. Whether you need a complete Bright cage unloading system with our Turnkey Installation, or would like to discuss an upgrade of your existing system to add optional equipment, contact your sales representative today.
Components
Incoming Conveyor
Hydraulically powered rollers bring the loaded cage to the transfer section to be unloaded into the receiving cage and onto the receiving belt.
Cage Tilt Section
Tilts loaded cage (60 degree angle maximum), allowing birds to exit the cage onto the receiving cage belt. Birds are evenly dispersed using stainless steel slides that are attached to the tilt cradle.
Receiving Belt Conveyor / Extension Belt Conveyor
The receiving belt receives birds from the stainless steel slides and conveys them to the extension belt. The extension belt conveys the birds from the receiving belt to the hanging belt. Belts available in either 88″ or 108″ wide.
Hanging Belt Conveyor
Controls the flow of chickens to the hangers. Places the chickens in front of the hangars at a comfortable level so they can be placed on the shackle line. The hanging belt conveyor is controlled by the last bird hanger with a pressure operated knee valve. The conveyor frames are constructed of stainless steel.
Lift Transfer Chain Conveyor & Outgoing Section
The lift transfer chain conveyor transfers the empty cage to the first outgoing conveyor. The first outgoing section begins returning the empty cage for reloading onto the transport trailer. (Optional cage washer can be added to this section.)
Outgoing Conveyor
Hydraulically powered rollers bring the empty cage to the end of the conveyor where it can be loaded back onto the trailer for reuse.
Operator’s Platform
Operator’s platform with standard control panel and stairs.
Safety System
See “Safety Features” listed below.
Finish
Hot Dip Zinc Galvanized
Safety Features
Bright Coop, Inc. is dedicated to Safety; that’s why every Bright Cage Unloading System comes standard with the following safety devices:
- Instructions and Warning Placards
- Safety arm at the end of the incoming conveyor
- (2) Red Flashing Lights
- Audible arms
- Safety Arm, Red Flashing Lights and Audible Alarm are activated by the interlock proximity sensors and advise the forklift operator not to load/unload cages
- Perimeter fencing that includes access gates with interlock proximity sensor to shut the complete system down (cage unloading and belt conveyors)
- Operator gate with interlock proximity sensor to shut the cage unloading system down while the operator is accessing the unloading area.
- Dumper section cradle lock with interlock proximity sensor.
- This device keeps the dumper section cradle from moving while doing maintenance on the system.
- (2) Electrical shutdown valves
- One valve shuts down the hydraulics of the unloading system
- One valve shuts down the hydraulics of the belt conveyor
Optional Equipment
Automated Hydraulic Door Closer
The automated cage door closer uses UHMW covered arms to close all doors at one time. This integrated operation helps reduce labor to close the cage doors and is also easier on the cages than most conventional door closers.
- Closes doors automatically
- Closer arms touch all doors at the same time
- UHMW covered closing arms reduces wear on doors
- Can be added to existing dumpers
- Heavy duty construction
- Extends doors and hardware life
- Allows operator to remain on operator platform
Hydraulic Power Unit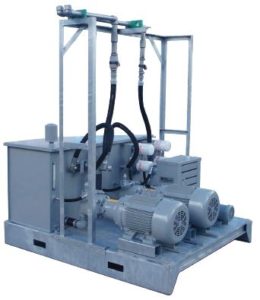
Bright’s Hydraulic Power Unit is a dual system allowing for a backup drive motor and pump to make sure your unloading system is never down.
- Two 60 GPM pressure compensating piston pumps
- Two High Efficiency BALDOR® 30 HP motors
- Optional 40 HP motors with 65 GPM pumps
- Air heat exchanger (water heat exchanger optional)
- Heater, thermostat controlled, 1500W
- Liquid level switch for safety shut down
- 0-3000 lb. Pressure Gauge
- Temperature switch (controls the cooling fan)
- Level / Temperature Gauge
- High pressure filter (protects components down stream)
- Double element High Efficiency return filter (10 micron absolute)
- 12 GPM Kidney loop system
- Galvanized base (standard)
- Steel painted tank (Standard) Stainless Steel (Optional)
Cage Washer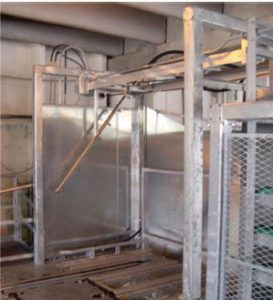
Bright’s Cage Washer utilizes a high-volume, low-pressure (HVLP) pump with an electric operated hydraulic spray boom. The water splash shield and trough are galvanized for longevity. Wash cycle times are adjustable according to production speeds. Pump uses 100 GPM at 150 PSI. The HVLP system has proven to be more effective than a high-pressure, low-volume system due to most plants using recycled water. The HVLP system uses large spray nozzles which will not clog as easily as the smaller nozzles used on high-pressure, low-volume systems.
Documentation
- Cage Unloading Sys Parts Manual Web (2019 – 06_22)
- Cage Unloading System Parts Manual 06_22 Web
- Cage Unloading System – Manual -2020 Web
- Cage Unloading System Operators Manual ENG Int – 2018
- Cage Unloading System Operators Manual SPA Int – 2018
- Cage Unloading System Operators Manual ENG_SPA 01_23
- Operator’s Manual – Lift Transfer Chain System – English
- Operator’s Manual – Lift Transfer Chain System – Española
- Operator’s Manual – Crossover Chain System – English
- Parts Catalog – Lift Transfer Chain (01/2016 to 2019)
- Parts Catalog – Lift Transfer Chain (Prior to 01/2016)
- Parts Catalog – Crossover Chain System – English